What makes capacitive linear encoders interesting for the high-tech and robotics sectors?
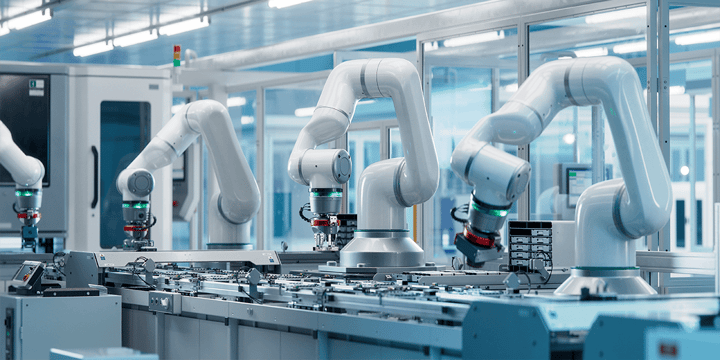
Developers of high-tech or robotic applications would do well to take a look at what a linear capacitive encoder can do for them. In fact, the advantages and versatility of this particular encoder variant are a perfect match for the challenges facing these kinds of applications.
A capacitive encoder functions on the basis of an electric field that is very precisely interrupted locally by a moving readhead. Displacements can be detected by measuring back the remaining field. Depending on the variant, it is also possible to define a specific position. When multiple tracks are integrated into the ruler of the encoder, this produces a unique signal for each position over the entire measurement length. This can also be done with an optical encoder for example, but since it is already a bit more expensive, an absolute measurement with this kind of encoder also carries a larger price tag.
Design freedom and shockproof
The beauty of capacitive technology is in the design freedom it gives developers. In fact, the distance between the ruler and the measuring head can be as much as 3 millimetres. With an optical encoder, the signal becomes less reliable at half a millimetre, but a capacitive encoder is much less sensitive to the size of the standoff. So that gives users greater alignment tolerances.
As a direct result, a linear capacitive encoder is highly resistant to shock and vibration. Variations in the distance between the ruler and the measuring head will not throw a spanner in the works quite so easily. Dust, dirt or magnetic fields also do not normally affect positioning with a capacitive encoder. Another point worth mentioning is the fairly wide temperature range of -40 to +85 degrees Celsius.
Of course, linear capacitive encoders are not suitable for all applications. While they achieve a very acceptable accuracy of about a micrometre, if sub-mu precision is required, optical encoders, for example, are the more obvious solution. Capacitive encoders also do not handle moisture or condensation very well. They work in environments with a relative humidity of up to about 90 percent, but above that the measurement system will need to be well protected against moisture.
Cable-free measuring head
Linear capacitive encoders are available in configurations where the moving measuring head is passive. That is to say, when there is no need to run a cable to that part of the system. The readhead is then just a small PCB with a very limited mass. In fast-moving systems, this offers advantages in terms of inertia in any case. But a passive measuring head also means no expensive flexible cables and cable chains that have to be run through the machine with slack, ensuring no wear on the moving parts. That means this kind of configuration is easier to integrate into a system design because the cables are only connected to the stationary section and can be neatly concealed within the machine structure.
And linear capacitive encoders don't just fit well into the high-tech world and robotic applications. The properties of this encoder type also offer a range of advantages for agricultural and horticultural technology as well as for medical and healthcare applications.
Would a capacitive linear encoder fit into your high-tech or robotics application?
Capacitive linear encoders accurately measure the position or displacement of an object. They are incredibly precise and offer a high level of design freedom due to their high installation tolerances. This makes them particularly interesting for high-tech and robotics applications. Does your application need this kind of capacitive encoder?
This whitepaper will help you get started. You will be comparing capacitive encoders to other encoder technologies. But you will also be going into more detail about capacitive linear encoders: from the various types of encoders through to the technical specifications.