Capacitive linear encoders offer new opportunities for integration
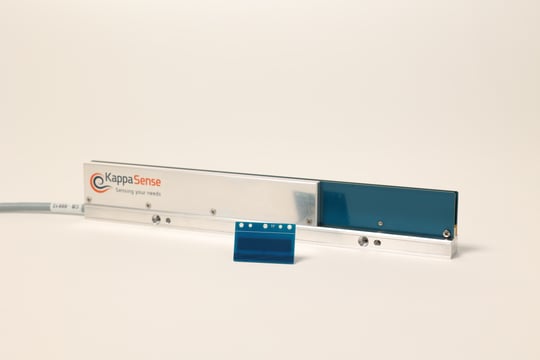
In the world of advanced technology, accurate measurement is essential for production systems to run smoothly. For positioning, this often comes down to deploying the most appropriate encoder for each situation. But there is so much choice; how do you determine which type best suits your circumstances and needs? A new partnership with KappaSense offers many additional options around capacitive linear encoders.
What is the function of a capacitive linear encoder?
A capacitive linear encoder is an advanced measuring instrument that can accurately determine the position or displacement of an object. The system consists of a scale (or ruler) with a series of precisely applied patterns and a measuring head that moves along this scale. The measuring head detects changes in capacitance due to the relative motion between the head and the scale. These changes in capacitance are converted into electrical signals, which are then translated into a digital readout indicating a position along the scale.
Their impressive accuracy and resolution make capacitive linear encoders often used in precision instrumentation and equipment, such as semiconductor manufacturing, microscopy, and precision workshops. Although they are sensitive to environmental factors like temperature and humidity, modern designs often incorporate compensation mechanisms to minimize these influences.
Mapping needs
To properly identify the needs of a potential user, knowledge of the on-site situation is important. What does that application look like? What exactly needs to be measured? What will be the location of the sensor? Is it inside or outside, movable or static, deep inside the machinery, or on the surface? An encoder excels at accurately measuring distances or position changes, but choosing the right method depends on the specific conditions of the application.
Sentech product manager Rob Kuijpers: "We often receive requests to develop modules that measure distances from a specific position. The diversity of approaches requires careful tuning to each company's specific situation."
Different types of encoders and techniques
In fact, there are numerous methods for making measurements. There’s a difference between rotary and linear encoders, and you can take the measurement absolutely or incrementally. In the latter case, the measurement starts from a fixed reference point, and the differences gradually increase. Moreover, different techniques are available, including optical, inductive, and capacitive encoders.
Read more about the different encoders here
Partnership with KappaSense
"For the capacitive linear encoders, there is one supplier that stands out head and shoulders above the rest, and that’s KappaSense, an Israeli company that is totally dedicated to this field of expertise," says Rob. "We are therefore very pleased that we were recently able to enter into a partnership with KappaSense." He points to the customer benefit, partly thanks to that company's extensive portfolio. Think of:
- The FLEXe encoder with excellent installation tolerances for alignment (compared to optical technology, the distance between the scale and the encoder can be as much as four times larger with capacitive technology),
- the FREEe encoder, where the controlled part is the statically mounted part, which has the advantage that the moving part has no cable,
- the µFREE encoder with transmitter and receiver on the same side (thus single-sided encoder-scale combination) and again no cable to the moving part,
- the XY encoder with feedback in one direction and, at the same time, full flexibility also in the other direction.
What also helps is that developments at KappaSense do not stand still, so numerous new applications can be fulfilled in the near future. For example, work is underway on the dual readhead for FREEe and µFREE, where multiple positions can be reflected simultaneously within the same measurement system. Stitching of measurement systems is also planned, with the moving part to be measured seamlessly transitioned into a connecting measuring range. In addition, there will be an XY encoder that provides position feedback in both directions.
In short, the agreement with KappaSense offers a wide range of possible use cases that would benefit from such capacitive linear encoder technology, benefiting for example these markets:
- industrial automation
- semiconductor manufacturing
- metrology & inspection
- medical equipment
- printing & packaging
- aerospace & defense
- electronics manufacturing
Technology-independent
Regardless of choice, the final solution must fit seamlessly into the customer's work process. Rob says: "We strive for technology independence and an assembly that can be logically integrated into the customer's existing systems. Often, this means we ask the supplier to adjust the standard product or take that up ourselves." As a result, the specific requirements, such as cables, brackets, or a certain cleanliness of a product, can vary from customer to customer. "Given the unique requirements of each user, different brands may even come together in one integrated module, all to ensure smooth and effective integration."